The work truck industry is in a constant state of evolution. From the trucks we drive to the way we load equipment to how we sign paperwork, very few operations look the way they did 20, 10, or even five years ago. Those who use liftgates on a daily basis will appreciate the innovations coming from Anthony Liftgates in 2023. Kurt Walker, Anthony Liftgate product manager, shares more below.
WHY SHOULD OUR READERS CONSIDER ANTHONY LIFTGATE AS AN UPFIT FOR THEIR FLEETS?
WALKER: Anthony Liftgates has been in the liftgate business since day one, dating back to our invention of the liftgate in 1941. Our goal is to make liftgates that are tougher and easier to maintain than anything else on the market. Plus, we take a very hands-on approach to our customers’ success to be sure every liftgate is well supported for its entire life on the road.
We offer a large line of standard products for many different applications, and since we manufacture the vast majority of our components in-house, we are able to entertain low-volume custom requests to help tailor a standard product to unique applications.
WHAT ANTHONY LIFTGATE PRODUCT PUT THE COMPANY ON THE MAP, SO TO SPEAK? WHY HAS THIS PRODUCT BEEN A WINNER FOR FLEET OWNERS?
WALKER: Anthony set itself apart from the rest of the pack in the 1980s building liftgates to a far more complete extent than what was done at the time. Anthony created a product that was ready to install far more quickly and was fully factory tested prior to leaving the plant. We called this concept “EZ Mount,” and it has now become the industry standard.
Also, Anthony pioneered the use of low-maintenance friction reduction materials at critical pivot and slide points, removing unnecessary parts to reduce maintenance cost. The replacement of rollers with slide pads in rail liftgates was an Anthony innovation that has now also become broadly accepted in the industry.
Our grease-free technology has proven reliable and cost effective for fleets looking for a dependable product that doesn’t require routine lubrication. Another great feature of these bushings is that their non-metallic bushings are completely impervious to corrosion. While a grease-type can quickly degrade due to corrosion and wear if the lubrication intervals are not met, this bushing technology handles the harsh environment of the road very well.
IS THERE A NEW PRODUCT COMING SPECIFICALLY FOR CLASS 6-8 TRUCKS?
WALKER: Certainly, the most exciting new product release in our long history will be the revolutionary ReGEN RailTrac heavy-duty rail liftgate. This is a product that absolutely smashes the performance benchmarks set by today’s hydraulic liftgates.
To frame how truly revolutionary this liftgate is, it helps to start with a basic understanding of today’s liftgates. Essentially all modern liftgates are powered by hydraulics that require electricity from a motor. These motors get their power from batteries onboard the vehicle.
This arrangement works well in many ways, but hydraulics do come with a few key drawbacks. Chief among them are energy consumption, risk of oil spills, sensitivity to extreme temperatures, and high maintenance costs. Further, the majority of the energy input to a liftgate is lost as it translates to a moving cargo platform, so they are notoriously abusive to truck batteries. Keeping these batteries charged can be a challenge, especially on trailers, since their added length and intermittent connection to the tractor only make the problem of inadequate power more pronounced.
Most attempts to solve the energy supply-demand mismatch of liftgates have focused on increasing the power supplied. The ReGEN takes a comprehensive approach to both sides of the equation, and it drastically reduces the amount of power demanded by the whole system. It employs a brand-new drive concept to replace the entire hydraulic system developed in exclusive partnership with Rise Robotics. The ReGEN can recover energy from a downward cycle, and the total energy input required to operate one is only between 10% and 50% of a hydraulic equivalent liftgate, depending on how it is loaded.
The ReGEN RailTrac is oil-free, so operators never have to worry about a broken hydraulic line causing a mess on their customer’s parking lot or somewhere on the road. Another fantastic benefit to this liftgate is that it is completely “connected.” Remote diagnostics are integrated with the system’s hardware, providing remote visibility to the system performance far beyond simply reporting battery state of charge or cycles.
HOW IS THIS NEW TECHNOLOGY INNOVATIVE?
WALKER: The technology inside this liftgate delivers hydraulic-like forces with incredible precision and at a fraction of the energy input. It also features premium, brushless motors and all solid-state relays as opposed to mechanical switches common in hydraulic liftgates. Both provide a big boost in reliability and longevity. There is truly nothing like the ReGEN on the market today.
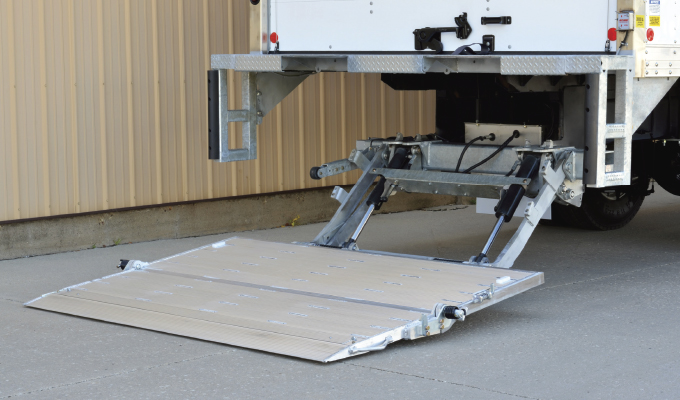
WHAT OTHER NEW PRODUCTS ARE IN THE LINEUP FOR THE FUTURE?
WALKER: We’ve spent years optimizing our aluminum platform offering on all TuckUnder™ models. Aluminum has grown in popularity over the years, replacing steel construction as the sole platform material in most commercial applications due to its corrosion resistance and lightweight rigidity. We saw an opportunity to elevate this area. These new aluminum extrusions that comprise new platforms deliver an extra 5% larger load area while shaving total installed weight of some models by up to 9%. Time consuming facets from the prior platforms were replaced with solutions engineered for throughput to maintain attractive lead times and scalability. Customers will begin seeing these new platforms in January 2023, with a full rollout through mid-year.
DOES THE INNOVATION EVER STOP AT ANTHONY LIFTGATES? WHAT ELSE IS COMING?
WALKER: We just released a new model called the MTU-GLR-XL for a freight customer who was looking to improve their ability to handle large cargo. At 85 inches by 90 iches, the load area of this liftgate is actually 50% larger than other liftgates in its class. It includes our patented Trifold Tuckunder Technology™ and is the first in a coming line of tuck-style liftgates with far larger platforms than today’s industry standards. These huge platforms will be a welcome addition to most vehicles because of the safety and versatility improvements that come with such a large load area.
ADDITIONAL THOUGHTS?
WALKER: I think it’s worth noting that every Anthony Liftgate is made in the USA using as much domestic material as possible. This has proved to be a sound strategy in the days of long port delays and component shortages. After the past few years of supply chain turmoil, many buyers are reconsidering their complex supply chains in favor of something closer to home. The past few years have certainly had their share of troubles, but we have been able to stay on the strong side of the production headaches plaguing factories around the world.
FOR MORE INFORMATION
Kurt Walker is the product manager at Anthony Liftgates. Before his time at Anthony Liftgates, Walker spent nearly three years with Caterpillar as a revenue analyst. Walker’s first role in marketing began with Anthony Liftgates in 2014. Walker is responsible for Anthony Liftgates’ TuckUnder product lines from end to end. In his five years as product manager, Walker has been responsible for three brand-new products and many optimization projects. Find out more about Anthony Liftgates, visit www.anthonyliftgates.com.