In the world of work trucks and vocational vehicles, proper tire inflation is a critical safety concern. Whether you’re managing a fleet of utility trucks, dump trucks or delivery vans, maintaining optimal tire pressure is crucial for vehicle performance, fuel efficiency and safety.
As technology advances, fleet managers are faced with an important question: What is the best way to maintain proper tire pressure in today’s work truck environment?
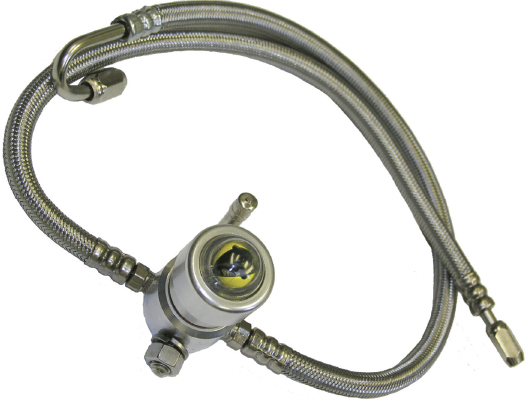
EVOLUTION OF TIRE PRESSURE MANAGEMENT
In the past, a quick thump of the tire was considered an adequate check. While this method might still be used by some, it certainly doesn’t qualify as a best practice in our modern, safety-conscious industry. The advent of tire pressure monitoring systems (TPMS) and automatic tire inflation systems (ATIS) has revolutionized how we approach tire maintenance in work trucks.
These technologies, which gained popularity in long-haul trucking, have now made their way into the work truck and vocational vehicle sector. At first glance, they seem to offer an ideal solution: constant monitoring and, in the case of ATIS, automatic inflation to maintain optimal pressure. However, as with many technological advancements, the reality is more complex than it appears on the surface.
PROMISES AND PITFALLS OF ATIS
ATIS promises a set-it-and-forget-it approach to tire pressure management. For work trucks that often operate in challenging environments—construction sites, off-road locations, or urban delivery routes with frequent stops—the appeal is obvious. Imagine a utility truck maintaining perfect tire pressure despite traversing rough terrain or a delivery van that never has to worry about tire pressure despite countless curb impacts.
However, the implementation of ATIS in work trucks comes with its own set of challenges:
Increased complexity: Work trucks often operate in harsh conditions. Adding an ATIS means introducing more components—additional air lines, connection points and electronics—all of which can be vulnerable to damage in these environments.
Potential for air leaks: Each additional connection point in an ATIS presents another opportunity for air leaks. In the dusty, debris-filled environments where many work trucks operate, these connection points can be particularly susceptible to damage and wear.
Seal integrity: Many ATIS use rotating seals which, over time, can wear or become misshapen. Exposure to temperature shifts can exacerbate the rotational wear, making seals shrink on cold days and expand on hot days. This combined rotational- and climate-induced seal deterioration can lead to air leaks, undermining the very purpose of the system.
Compressor strain: ATIS rely on the vehicle’s air compressor to maintain tire pressure. In work trucks, which may already be using compressed air for various tools or systems, this additional demand can lead to increased compressor run time, higher fuel consumption and accelerated wear on the compressor itself.
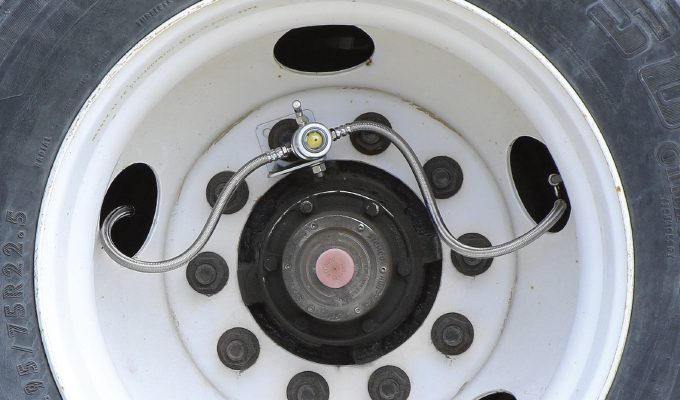
HIDDEN COSTS OF COMPLEXITY
Consider a scenario common in the work truck world, a municipal waste collection vehicle starts its route early on a cold fall morning. The ATIS light is on, indicating the system is working to maintain pressure. The ATIS seals are cold and constricted early in the route and as the day wears on and temperatures rise, the seals expand, slowing the leak. The driver, relying on the ATIS, may not realize that the failing seals are chronic cause of underinflation during the early part of the route, leading to increased wear and reduced fuel efficiency.
Moreover, the complexity of ATIS can lead to a false sense of security. Drivers and operators of work trucks, often pressed for time and focused on their specific jobs, might neglect regular visual inspections, assuming the system will take care of any issues. This can lead to missed early warning signs of tire damage or wear that go beyond simple pressure management.
THE COMPRESSOR CONUNDRUM
In the world of work trucks, every bit of engine power matters. Whether it’s a boom truck needing to operate its hydraulics or a refrigerated delivery van running its cooling system, auxiliary power demands are always a concern. Adding ATIS to this mix means more frequent and longer compressor run times.
Break down the impact.
Fuel consumption: Increased compressor usage means higher fuel consumption. For a single truck, this might seem negligible, but across a fleet of work trucks, it can add up to significant additional fuel costs.
Maintenance costs: More frequent compressor usage leads to faster wear and tear, potentially increasing maintenance frequency and costs.
Downtime: If an ATIS fails due to a leak or component failure, it could lead to unexpected downtime, a critical issue for work trucks that are often on tight schedules.
Future considerations: As the work truck industry begins to explore electric and hybrid options, the power demand of systems like ATIS will become an even more crucial factor in vehicle range and efficiency calculations.
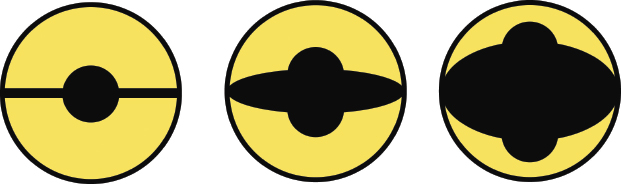
SIMPLIFYING TPMS FOR WORK TRUCKS
Given these challenges, there’s a strong argument for simpler, more robust tire pressure monitoring solutions in the work truck sector. Link Mfg., developed the Cat’s Eye system to provide clear, visual tire pressure monitoring without the complexity of fully automatic systems.
How it works in a work truck context.
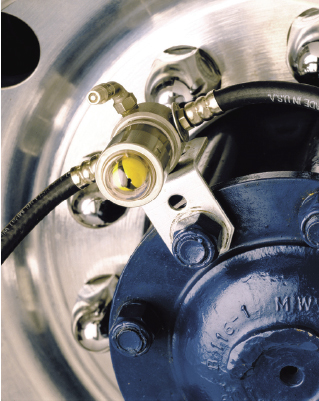
Installation: The system is ordered pre-set to the desired tire pressure and is simple to install. For a typical work truck with dual rear tires, two lines connect both valve stems to the Cat’s Eye, equalizing the pressure between the tires. The system also provides a single fill point for both tires, and compared to an ATIS, makes tire changes much easier.
Visual indicator: Instead of focusing the operator’s attention on an indicator light, it directs their attention to the actual tire system, promoting best tire maintenance practices. The system features a yellow, easy-to-read gauge. When proper pressure is maintained, the pupil-like gauge constricts to a thin black line. If pressure drops, the pupil dilates, providing an immediate visual cue to drivers or maintenance staff.
Dual tire protection: In dual tire setups common on many work trucks, the system maintains equal pressure between tires. If one tire experiences a sudden pressure loss, an internal check valve prevents the other tire from losing pressure, a crucial safety feature for work trucks often carrying heavy loads or operating in challenging conditions.
Simplicity and durability: With no electronics or complex mechanisms, the system is well-suited to the rugged environments many work trucks operate in. It’s less susceptible to damage from debris, impacts, or harsh weather conditions.
REAL-WORLD APPLICATION
Imagine a fleet of municipal service trucks equipped with the Cat’s Eye system. Each morning, during the pre-trip inspection, drivers can quickly glance at the indicators on each wheel. The more wheels a vehicle has, the more time savings value this simple, vision-based system provides. A fully constricted pupil gives them confidence that tire pressure is optimal. If they notice a dilated pupil, they know to check and adjust the pressure before starting their route.
Throughout the day, whether the truck is at a work site or making stops around the city, periodic visual checks take just seconds. This simplicity encourages more frequent monitoring without adding significant time to the driver’s routine.
For fleet managers, the system simplifies maintenance schedules. Instead of dealing with complex ATIS components, they can focus on regular tire inspections and replacements. The equalized pressure between dual tires also helps extend tire life and improve fuel efficiency, critical factors in managing fleet operating costs.
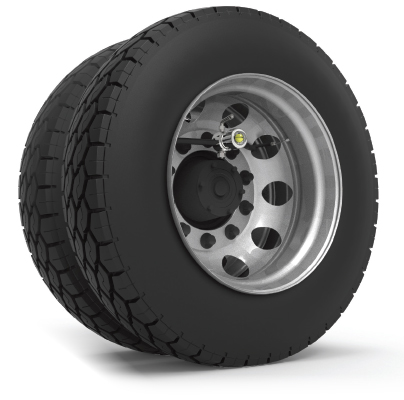
SIMPLY BETTER TIRE MANAGEMENT
In the ever-evolving landscape of work truck technology, it’s crucial to strike a balance between innovation and practicality. While ATIS might seem like a comprehensive solution, the added complexity and potential issues may outweigh the benefits, especially in the demanding environments where work trucks operate.
A simpler TPMS system offers a middle ground. It provides clear, actionable information about tire pressure without the drawbacks of a fully automatic system.
This approach aligns well with the needs of work truck fleets.
Reliability: Fewer components mean fewer potential points of failure.
Cost-effectiveness: Lower initial cost and reduced maintenance requirements.
Simplicity: Easy for drivers and maintenance staff to understand and use.
Durability: Better suited to withstanding the rigors of work truck operations.
As we continue to advance in vehicle technology, it’s important to remember that sometimes, simpler solutions can be the most effective. In the case of tire pressure management for work trucks, a straightforward, visual system can provide the necessary information without unnecessary complexity.
By focusing on simple, reliable tire pressure monitoring, fleet managers and owner-operators can ensure their work trucks remain safe, efficient, and ready for the demanding tasks they face every day. After all, in the world of work trucks, it’s not just about keeping the wheels turning, it’s about keeping them turning safely and efficiently, job after job, mile after mile.
About the Author
Mark Molitor brings over 27 years of experience with engineering in the heavy-duty trucking industry to his position as senior product manager – chassis suspensions for Link Mfg. Prior to his appointment at Link, Molitor held several roles with SAF-Holland including: VP product engineering, Americas and VP product engineering, powered vehicle systems business unit. His educational credentials include a Bachelor of Science degree in mechanical engineering from Western Michigan University.
To learn more, visit www.linkmfg.com/products/specialty-products/cats-eye.