You may be at a remote jobsite, working on an isolated utility line, in a quarry or out in a farm field when the unexpected happens. Maybe you need access to compressed air to address the problem, maybe it’s AC power or welding capabilities. It might be the type of power required to complete your duties in the field, or it might be what you need just to limp back to home base for more comprehensive repairs. Whatever it is, the demand for mobile power is only growing.
“We first saw the need for mobile air back in 1972,” said John Dunn, strategic sales representative, Vanair. “Our solution was the truck-mounted 185 CFM underdeck rotary screw air compressor, and that innovative design was the first to consolidate the features of an engine-driven, tow-behind rotary screw compressor onto a truck frame.”
The design harnessed the truck’s engine to power the compressor through the vehicle’s power take-off (PTO). The benefits of this system soon resonated throughout the industry, as it liberated the vehicle’s hitch, reduced weight, expanded valuable bed space, decreased maintenance and insurance expenses, and enhanced mobility.
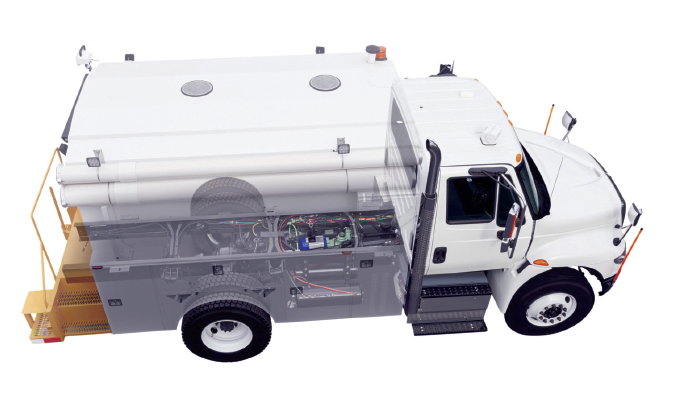
OVER THE YEARS
Since their inception, Vanair’s Underdeck systems have evolved. Historically, users of Vanair’s PTO-driven Underdeck systems, whether it’s a multifunction Genair System or V2 Multi-Drive Air Compressor/Hydraulic Pump Pad System or V3 Multi-Drive Air Compressor/AC Generator/Hydraulic Pump Pad System, have been utility companies, utility contractors and municipalities.
“Vanair has also seen a huge increase in the last 10 years, with all of those industries using air excavation,” says Dunn.
Dunn said that the products have supported air excavation well and that its core user groups are adopting air excavation rapidly. At the same time, the company has also seen a move toward trenchless boring.
2020 VISION
The year 2020 marked a watershed moment for the industry. Vanair introduced a tank and manifold design. The reimagined system housed all control equipment in one place, and reorganized oil filters, pressure valves and scavenge lines. This design consolidated multiple components into a single, factory-assembled unit, using JIC fittings that reduced potential oil leak points by over 80 percent. The redesign also decreased installation times by 10 to 15 percent.
The shift eliminated the random placement of components under the vehicle, which previously varied from one installation to the next. By moving to a uniformed and streamlined assembly, this improved its reliability and ease of maintenance. This reengineering not only simplified the system but also cleaned up the underside of vehicles, standardizing the installation process and ensuring uniformity across all units.
“With the change, every single system is the same, bringing what I call ‘uniformity of build’ to the equation,” says Dunn. “This uniformity is crucial, not just for consistency in build quality but also for reducing the time and cost associated with the installation and maintenance of these systems.”
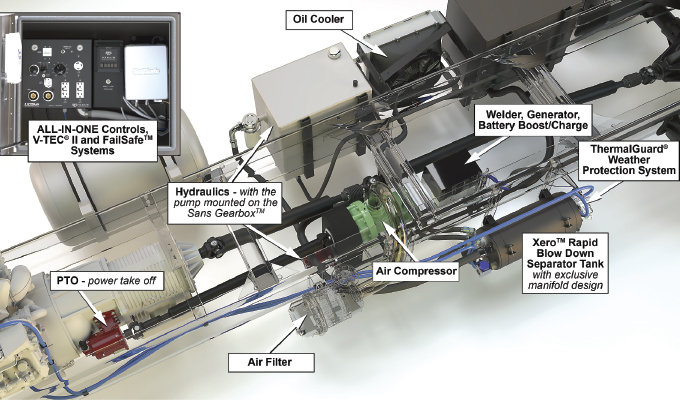
REAL-WORLD BENEFITS
Along with structural and design improvements, 2020 also saw Vanair introduce several patented features. One is the FailSafe Dual Sensor Redundancy System, a standard offering that provides backup sensors to ensure continuous operation, even if a primary sensor, such as a thermistor or transducer fails.
“Another notable innovation and standard offering were the UltraLife Air/Oil Separator Element, a coalescing element which is found inside the tank. It’s designed to double the regular service life significantly—up to 6,000 hours, or roughly 12 to 15 years for most utility companies,” says Dunn. “This extended functionality, often far surpassing the lifecycle of the vehicle itself, drastically reduces the need for preventive maintenance, thereby lowering long-term operational costs.”
The system now also includes a zero-valve inside the tank, since summer 2023. This valve plays a crucial role in reducing blowdown time and minimizing oil carryover when the system shuts down, which extends the system’s longevity and ensures cleaner air output.
The ThermalGuard, an optional feature, utilizes engine coolant to preheat the oil in the air/oil separation tank, significantly speeding up the time it takes for the system to reach operational temperature. This functionality is beneficial in varying climates, as it aids in moisture management within the compressor system, ensuring efficient operation regardless of extreme hot or cold weather conditions.
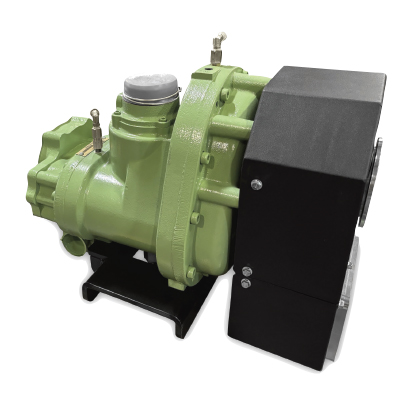
ALL IN
Unveiled at the NTEA Work Truck Week in March 2024, the Underdeck ALL-IN-ONE System combines six functions into a single compact unit. This system includes a 125-185 CFM rotary screw air compressor, a 10kW generator, a 330A welder, 12V, 24V and optional 36V and 48V battery boosting capabilities, 12V-24V and optional 36V and 48V battery charging capacity and up to 30 GPM at 2000 PSI of hydraulic-driven power. Its multifunctionality allows the system to cater to a wide array of operational needs, from construction sites to utility repairs.
“This change addresses several critical aspects of power delivery systems — weight, noise, and power output,” says Dunn. “With the new cog-belt-driven pulley design, we’ve increased power by 50 percent and can deliver up to 30 GPM at 2,000 PSI of hydraulic power. This not only surpasses our previous models but also sets a new industry standard for efficiency and output.”
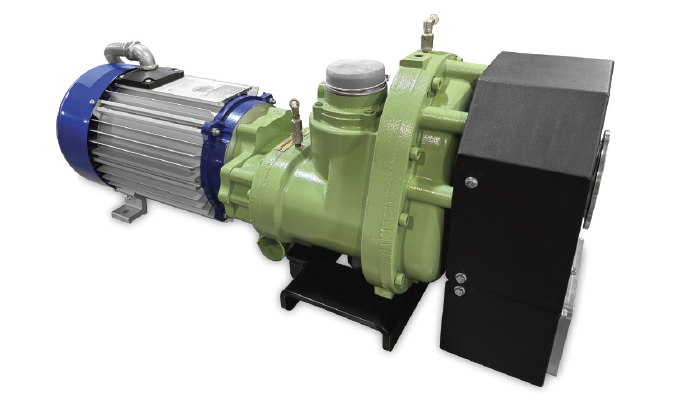
ADVANTAGES
The offers weight savings — potentially replacing up to four separate machines, which could mean a weight reduction of 1,500 to 2,500 pounds. The entire system is designed to be mounted under the vehicle’s body on the frame rail, which optimizes weight distribution and preserves valuable cargo space. The placement also enhances vehicle stability and leaves the load area unobstructed for other uses.
The system also fits a broad range of chassis sizes, if the configuration supports an 84-inch cab-to-axle ratio and the necessary PTO accessibilities, it will serve everything up to a Class 8 vehicle.
“The application breadth for the Underdeck ALL-IN-ONE is so vast, it’s almost incalculable,” says Dunn. “People don’t realize that they need this equipment until they hear about it – or see it in action – after that it literally sells itself.”
FOR MORE INFORMATION
To learn more about Vanair and its Underdeck Systems, visit www.vanair.com.