Many vehicles including delivery and vocational trucks run unloaded or mostly unloaded for half of their working lives. Their suspension geometry and the types of springs they use are the two biggest influences on driver comfort and cargo and equipment protection. Both factors should be considered when specifying a suspension system for work truck applications.
According to Mark Molitor, senior product manager of chassis suspensions for Link Mfg., Ltd, torque reactive and non-torque reactive are the two basic categories of suspension geometry. Torque reactive suspensions are most often comprised of steel springs and are among the earliest form of vehicle suspensions dating back to the days of horse-drawn wagons. Non-torque reactive suspensions employing air springs have been around for about three decades and offer considerable advantages over their steel predecessors. The air pressure for these systems is generally supplied via an engine-driven compressor unit.
Both types of springs can provide a vehicle with adequate suspension, but a non-torque reactive air suspension will provide the most comfort for a driver and crew and the highest level of cargo and overall asset protection.
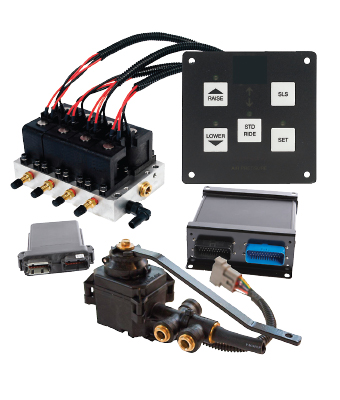
AIR APPARENT
Air suspensions reduce the frequency and severity of road vibration throughout the vehicle, which means less wear and tear. With an air suspension, drivers experience a far smoother and more stable ride, as well as a more comfortable driving experience.
A suspension’s vertical stiffness can also play a role in the process. With all steel spring suspensions, the stiffness is generally tuned to provide the smoothest ride when the vehicle is fully laden. Once cargo is offloaded, the axles of unladen vehicles can start to bounce, as uneven road conditions excite the tires and then resonate throughout the entire vehicle.
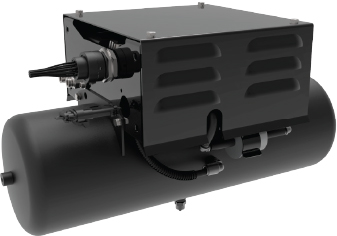
CONTROL & BALANCE
Fleets focused on driver comfort and with applications dealing with important cargo or equipment will typically specify an air suspension system. These systems will adjust the suspensions’ stiffness as the load changes by means of height control valves. Height control valves can also help maintain a uniform ride height when a vehicle’s cargo becomes unbalanced or lopsided, as can occur as cargo is offloaded.
The vast majority of air suspension systems use a mechanical valve that employs a lever. As the suspension articulates in relation to the chassis, the lever toggles and either opens or closes ports that inflate or exhaust air from the air bags on either side of the suspension.
“However, mechanical valves can become confused by simply encountering a pothole in the road, causing the system to overreact, creating a temporary imbalance while the mechanical system recalibrates itself,” Molitor says. “This means increased compressor run times and ultimately, additional fuel use.”
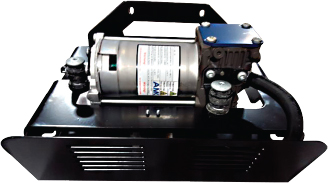
SMARTER CONTROL
Link’s Smart Air Management System (SAMS) now brings state-of-the-art digital control to air spring suspensions to a variety of work truck platforms. With SAMS, gone are the delayed response times and over or under air bag inflation corrections associated with mechanical height control mechanisms. SAMS’ electronic control unit, (ECU) responds dynamically, hundreds of times a second to road conditions, cargo weight distribution, and more.
“SAMS is a sophisticated electronic height control system that addresses not only ride height, but auto leveling and active load management,” says Brian Kujala, vice president business development for Link Mfg., Ltd. “SAMS enables virtually any Class 3 to 6 vehicle with an air suspension system to have the best and most consistent ride quality available in the industry.”
With Link’s SAMS, users have total air management capabilities with diagnostic monitoring, LED indicator, touch screen interface, and USB connectivity. With the SAMS user interface, drivers can override a vehicle’s set ride height to raise and lower its chassis at low speeds when desired.
Users can also raise and lower the rear of a vehicle for loading and unloading. Limited only by shock absorber travel, the system can be used to maintain stability and keep the deck of a vehicle more flush with a loading dock while heavy forklifts cross their thresholds. Vehicle fuel economy is also improved through greater ride height accuracy, resulting in reduced compressor run times through the avoidance of unnecessary valve actuations.
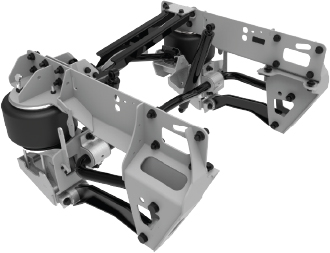
A NATURAL FIT
SAMS is compatible with virtually any commercial air ride suspension system and upfits easily. However, for those who want to convert from leaf spring to air, Link has the UltraRide® suspension with its SAMS option. Link’s UltraRide® is a total conversion suspension that replaces a standard leaf spring suspension system on vehicles with a GVW of up to 19,000 lbs.
Now available with SAMS, the UltraRide® air suspension provides increased operator and passenger comfort, ease of access, and overall safety. With an additional cross member, UltraRide® ensures proper alignment, increased stability, and reduced frame stress across multiple applications.
HIDDEN COSTS
Engine-driven air compressors—often located in difficult-to-access locations—drive most traditional air suspension systems.
“Many folks are unaware of the replacement costs associated with engine-driven air compressors,” Kujala says. “In many cases, the radiator must be removed, and in some instances much more extensive work must be done to simply replace a system. I know one bodybuilder that was spending four times the cost of the new engine-driven compressor unit just trying to get it installed.”
Hydraulic systems have also gained popularity in the market. However, their system architecture, complexity, initial cost, maintenance, repairs, and replacement cost can each be prohibitive in their own right.
“When it comes to reliability, serviceability, and simplicity, SAMS is a logical, time-tested choice,” Kujala adds.
SYSTEMIC APPROACH
Link’s family of SAMS Air Control Systems are available in easy-to-install kits that make upfitting simple and convenient. SAMS units work seamlessly with existing onboard air systems and also come as a bolt-on kit with a dedicated compressor. SAMS kits may be ordered in ether a tankless version with a direct-drive compressor and no air reservoir or with an air tank.
Fleets and bodybuilders can order vehicles without the optional engine-driven compressor units and install a hassle-free SAMS system almost anywhere. Not only can they offset the cost of the SAMS system, but they can avoid the high cost of repairs and replacements later.
SAMS fully automated air control systems are available in two work-truck-ready versions. The tankless SAMS TL System is perfect for light-duty applications and the SAMS 2 Way System fits most Class 1 to 6 applications.
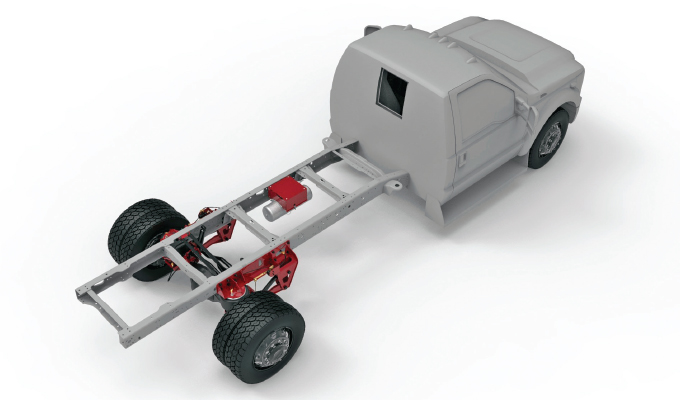
AN OIL-FREE FUTURE
Whether to achieve sustainability targets, to comply with regulations, or to maintain good corporate citizenship, US fleets are preparing to decarbonize. The SAMS system has significant experience with zero-emission vehicles (ZEV) beginning with the electric bus market. SAMS has delivered big suspension benefits with little power consumption overhead, and it’s ready to do so in the commercial ZEV environment.
“With SAMS, ZEV fleets will enjoy enhanced driver safety and cargo security, increased power savings, and operational efficiencies including reduced compressor run times,” Kujala says. “Vehicles with SAMS will travel longer distances between charges and will respond to geofencing and other location- and circumstance-based action triggers that will be part of that new environment. Whatever’s coming next, Link will be there with suspension solutions to meet it.”
FOR MORE INFORMATION
Find out more, visit www.linkmfg.com.