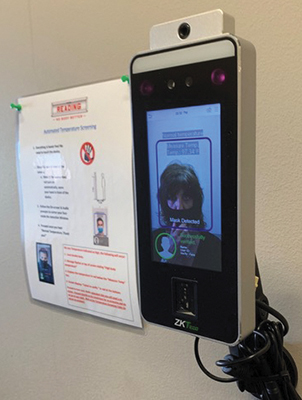
MWS: WHEN DID YOU START PLANNING FOR A COVID-19 INCIDENT?
BRODIE: Our leadership was actually in the middle of discussing how we would react in the event of a COVID-19 case at one of our facilities when there was a false alarm at our Maryland facility. It happened before states started going into lockdown and before it was officially declared a pandemic. It turned out not to be COVID, but that was a really critical moment for us. Everyone in leadership realized that we couldn’t wait for a case to hit and then react. That incident started a process of trying to anticipate what could happen and planning out our responses, which ultimately developed into our internal COVID-19 task force.
MWS: WHAT DID YOU LEARN FROM THAT FALSE ALARM?
BRODIE: Failing to plan is planning to fail. Beyond planning ahead, having a dedicated task force is critical. A task force centralizes decision-making and the flow of information so there’s clarity and accountability. For a manufacturing company, a good COVID-19 task force should include site leads, human resources, and health and safety departments. Our task force includes about 40 people from across departments, and we decided early on that meeting every morning during the work week was essential.
Conditions on the ground change frequently, and guidance from health care authorities like CDC, OSHA, and state health departments changes almost daily. You have to meet often to respond to rapidly changing conditions. At a typical task force meeting, we go over changes in guidelines, review potential cases and test results, and talk about employees who need to be tested. It’s really an extension of the daily management techniques that many manufacturers (including Reading) use in their regular business operations.
MWS: HOW CAN MANUFACTURING COMPANIES PREPARE FOR A POTENTIAL INFECTION?

BRODIE: The practices have helped avoid transmission at our 13 facilities across the US so far. But we had to be ready for the possibility of transmission, so we turned to the lean manufacturing principles we use in our plants for help. The task force created a set of standardized practices that can be implemented in the event of a potential exposure or incident. This “decision tree” gives the site leads a very simple playbook that tells them how to react appropriately no matter where an incident happens, who is on shift, or whether an executive is available. That standard has been in place across the company since March, and we’ve made eight iterations of it as guidance as regulations have changed.
COMING UP
Next month we’ll wrap up our interview with Jim Brodie as he answers questions on physical changes in Reading’s operations, additional measures to address the pandemic, and using technology to slow the spread.